Development basis and background
In recent years, four axis aircraft and unmanned aerial vehicles have been considerable development. If we can grasp the regional advantages and market opportunities, carry out the supporting development of permanent magnet DC micro-motors based on quadcopter, and form a high-performance DC iron core micro-motor industry for quadcopter covering various models, it is expected to quickly meet the various needs of customers and meet the needs of market demand, thus effectively promoting the improvement of the company's performance;
On the other hand, from the perspective of market expectations, the quadcopter, as one of the drones, has received more and more attention from all parties with its wide application in recent years. As the power source of the four-axis aircraft, the permanent magnet DC micro-motor plays a key role in realizing the characteristics of the four-axis aircraft such as fixed-point hovering, vertical take-off and landing, stable and reliable flight, high flexibility and good safety.
Due to the continuous emergence of new materials and the higher requirements and price requirements of users for quadcopters, quadcopter manufacturers have put forward higher performance requirements and lower price requirements for permanent magnet DC micromotors. There are currently two types of motors used on four-axis aircraft:
① Brushless DC motor. Large power-to-volume ratio, high efficiency, low noise, high operational reliability and long life. However, the electronic commutation structure is complex, which requires high control drive system and speed control system of the aircraft; the price is high.
② DC motor with carbon brush. Widely used, good speed regulation characteristics, simple control, smooth operation, low price. However, the power-to-volume ratio is small, the efficiency is low, the reliability of carbon brushes and commutation is poor, the noise is large, the electromagnetic interference is large, and the life is low.
Through the comparison of the above permanent magnet DC micromotors, our company is committed to developing a carbon brush DC motor with low price, high performance, high reliability, improving power-to-volume ratio, efficiency and life as much as possible, and controlling noise, so as to optimize the company's revenue contribution structure, ensure that the company's products lead the industry product trend, and achieve a new level of enterprise scale, in line with the company's long-term development plan.
Main R & D contents and results
R & D content:
1, suppress electromagnetic interference, so that EMC meets the requirements. Since the four-axis aircraft is operated by wireless remote control, there is no doubt that there are strict requirements for electromagnetic interference. By adding a strontium titanate ring varistor at the commutator end of the micro-motor rotor, the commutation spark and arc are suppressed, and the harmonic electromotive force is reduced; the carbon frame is pressed, and damping strips are added on the carbon frame at the same time, and MS395A.2 damping glue is added at the bending part of the carbon frame to prevent the high frequency component from being too large due to the trace runout of the carbon frame, causing excessive interference power.
2. Improve the service life and meet the requirements of high speed and low noise of the motor. Based on the four-axis aircraft fixed-point hover, vertical landing, stable and reliable flight, high flexibility, the use of micro-motor directly drive the four-rotor high-speed rotation mode, the speed of the micro-motor is very high, no-load speed up to 65000rpm or more. By replacing the copper-based oil cup with iron-copper-based oil cup, the surface hardness and crushing strength (>200Mpa) are increased, and the oil content (>20%) is increased. The purpose of replacing copper carbon with increased silver carbon is to improve the hardness of the carbon brush and increase the contact area between the carbon brush and the commutator surface. the harder the carbon brush, the greater the contact resistance, the greater the contact pressure drop and the smaller the spark, the noise is also smaller (<60dB); through the above measures, the service life of the motor can be significantly improved and the noise can be greatly reduced.
3. Improve power-to-volume ratio and efficiency. Use outer diameter φ8.5mm rotor instead of φ8.2mm rotor. By using MATLAB software to simulate and calculate the power of different rotor structures of micro-motors under the same magnetic flux density, using PRO/E and AutoCAD software to design, the outer diameter φ8.5mm rotor is developed, thus improving the power-to-volume ratio of the motor under the same external conditions, reducing the load current and improving the efficiency.
4. Strengthen the physical performance of the motor. Due to the high speed of the motor, there are higher requirements for the physical properties of the motor. Our company has replaced the original common rubber cover with glass fiber high temperature resistant material (PA66 G30) to meet the requirements of higher temperature rise under high motor speed and heavy load. The riveting of the motor shell adopts direct riveting method to meet the strength of the quadcopter falling at low altitude. The rotor coil of the micro-motor is fixed with "600LG" glue to prevent the enameled wire of the rotor from breaking away from the wire package due to the centrifugal force generated when the micro-motor is high speed.
R & D Results:
1. Form a supporting scale capable of producing more than 1 million motors per year, develop 4 series of permanent magnet DC micromotors based on quadcopter, and create 25 new jobs;
2. Further consolidate the company's position in the industry, improve the company's ability of independent innovation, achieve the growth of the company's sales scale by more than 10%, and improve the company's market competitiveness;
3. A high-performance motor with super-force characteristics has been formed to fully meet the customized needs of high-end customers in the model and the needs of some foreign customers;
Legend of developed motor
Application Legend
Key words:
Previous Page
Previous Page
Guangdong Chaoli Motor Co.,Ltd.
Here is the title one h1 placeholder text
Address: Xingye East Road, Laimei Industrial Zone, Chenghai District, Shantou City, Guangdong Province
Shenzhen Sales Division
Name: Ms Hu
Mobile:(86) 138 2352 5969
Telephone:(86-755)2721 9096/2721 9696
Mailbox:szcl@chaolimotor.com
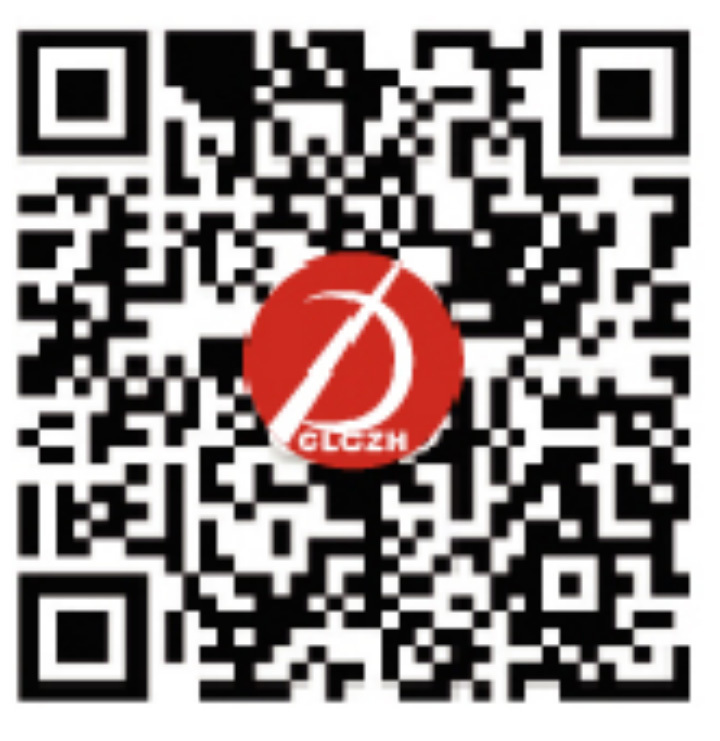
WeChat QR Code
Name: Mr. Cai
Mobile: (86) 136 7045 7762
Telephone:(86-754) 8696 2232
Mailbox:Henry@chaolimotor.com
Website:www.chaolimotor.com
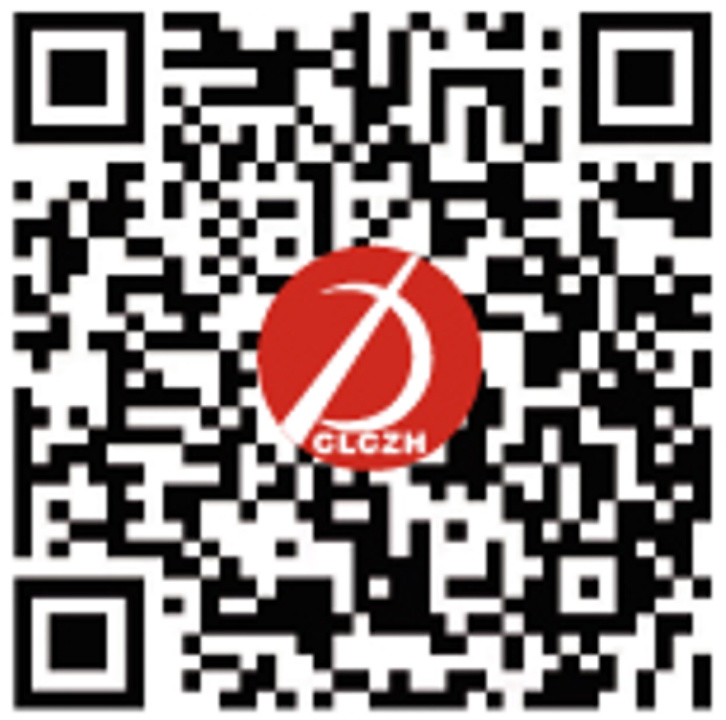
WeChat QR Code
Name: Mr. Chen
Mobile:(86) 156 0271 1777
Telephone:(86-754) 8696 2230
Mailbox:cl@chaolimotor.com
Website:www.chaolimotor.com
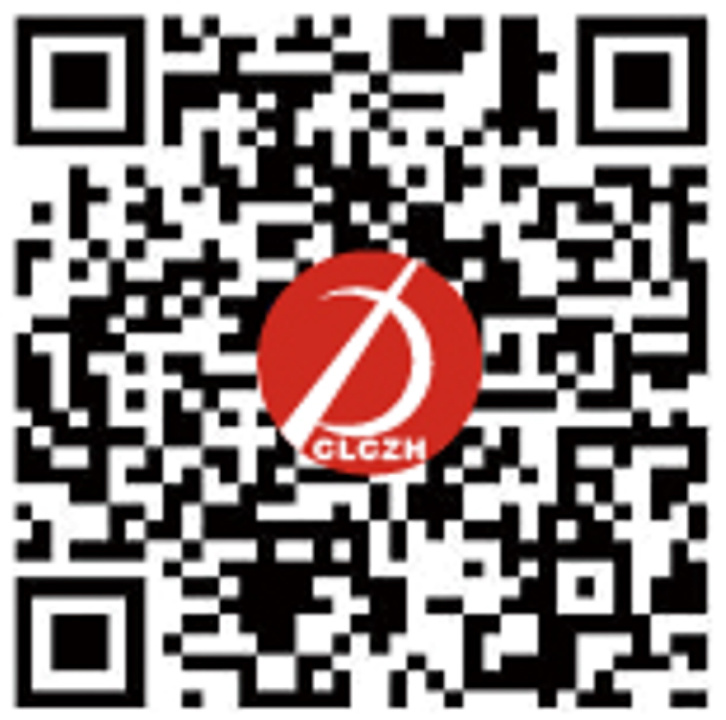
WeChat QR Code
Main Products
Can't find the service you are looking for? Contact us!
If you need to inquire about our products, please leave your email to us and we will contact you within 24 hours.