Development basis and background
The motor, also known as the motor, is an electromagnetic device that realizes the conversion or transmission of electrical energy according to the law of electromagnetic induction. The motor generally includes a casing, a front end cover, a rear end cover, and components such as a stator, a rotor (armature), a bearing, and a brush assembled in the casing. The main role of the casing is to fix and protect the internal stator, rotor, bearings, brushes and other functional components, so as to form a complete electromagnetic induction area according to certain accuracy standards and technical specifications, and realize the smooth conversion of energy from electrical energy to mechanical energy. It can be said that the performance of the casing is one of the important factors reflecting the control accuracy and service life of the motor.
At present, the fixing method of the motor housing and the end cover usually adopts a bayonet on the housing, and the end cover is provided with a clamping block. After the clamping block of the end cover is put into the bayonet, the edge of the housing is punched on both sides of the bayonet with tools, so that the housing part on both sides of the bayonet is pressed against the outside of the end cover, and the housing and the end cover are fixed. However, in this existing motor, the housing and the end cover are not firmly fixed, and the overall rigidity of the motor is low. When the motor is in use, the end cover often shifts and shakes, and it is easy to generate large vibration to generate noise. Affect the normal use of the motor; it is inevitable that the motor will fail during use, and the end cover needs to be removed when the failure occurs, which brings inconvenience to the maintenance of the motor.
Main R & D contents and results
R & D content:
1. Research on optimization design technology of motor end cover structure based on low noise
A positioning structure of a motor casing end cover is developed, which has simple structure, stable positioning and can realize rapid positioning and installation. It comprises a body and an output shaft rotatably arranged on the body, and the body comprises a casing, an end cover and a snap ring. The positioning and fixing of the snap ring are realized. The end cover is inserted on the casing. Through the cooperation of the bayonet and the clamping block, the threaded holes between the snap ring and the end cover are coaxially aligned, and the snap ring and the end cover are fixed by screws. Connection can effectively prevent the end cover from shifting and shaking during the working process of the motor, and effectively reduce the noise during the operation of the motor.
2. Research and development of high energy product rare earth permanent magnet micromotor materials;
From the perspective of the system and customer performance requirements, the optimal combination of motor model and magnet is carried out to determine a variety of motor types, and more importantly, the balance is achieved at the contradictory point of motor torque and speed, and then the optimal and most reasonable price matching scheme is obtained, which meets the different customized needs of different customers and provides an effective path to maximize the efficiency of the motor, the efficiency can be increased by more than 5%.
3. A fully automatic assembly production line has been developed, which is fully integrated with end cover adaptive adjustment to automatically produce stator assembly, assembly and testing processes. The production line is equipped with advanced equipment, high degree of automation, and good production continuity; reliable performance, high efficiency and safety, environmental protection and energy saving. At the same time, it is also very convenient to operate, adaptable, and able to adapt to the expanding market demand.
R & D Results:
1. Develop a series of micro-motors with low noise, high energy density, strong practicability and high cost performance, which fully meet the needs of electric tools and small household appliances. Set up an automatic assembly production line, each production line can produce 10000 motors per day, and the annual production capacity can be about 2.5 million. Significantly enhance the company's resilience and competitiveness, while promoting the processing and production of regional micro-motors, driving the development of the local micro-motor industry, and playing a positive role in driving the local economic development.
2. Compared with the old model motor, the adaptive adjustment fast positioning structure low noise micro motor can achieve higher efficiency and greater power/weight ratio. The rated output power is increased by 0.5 times, the power density is increased by 1 times, and the noise is reduced by 10dB(A weight), which realizes the thinning, high output and low noise of the motor.
Legend of developed motor
Application Legend
Key words:
Guangdong Chaoli Motor Co.,Ltd.
Here is the title one h1 placeholder text
Address: Xingye East Road, Laimei Industrial Zone, Chenghai District, Shantou City, Guangdong Province
Shenzhen Sales Division
Name: Ms Hu
Mobile:(86) 138 2352 5969
Telephone:(86-755)2721 9096/2721 9696
Mailbox:szcl@chaolimotor.com
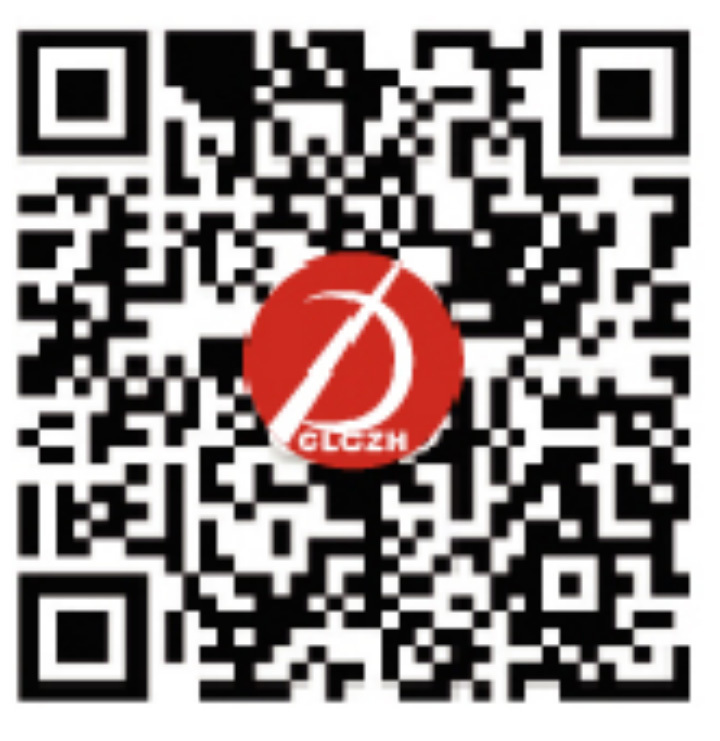
WeChat QR Code
Name: Mr. Cai
Mobile: (86) 136 7045 7762
Telephone:(86-754) 8696 2232
Mailbox:Henry@chaolimotor.com
Website:www.chaolimotor.com
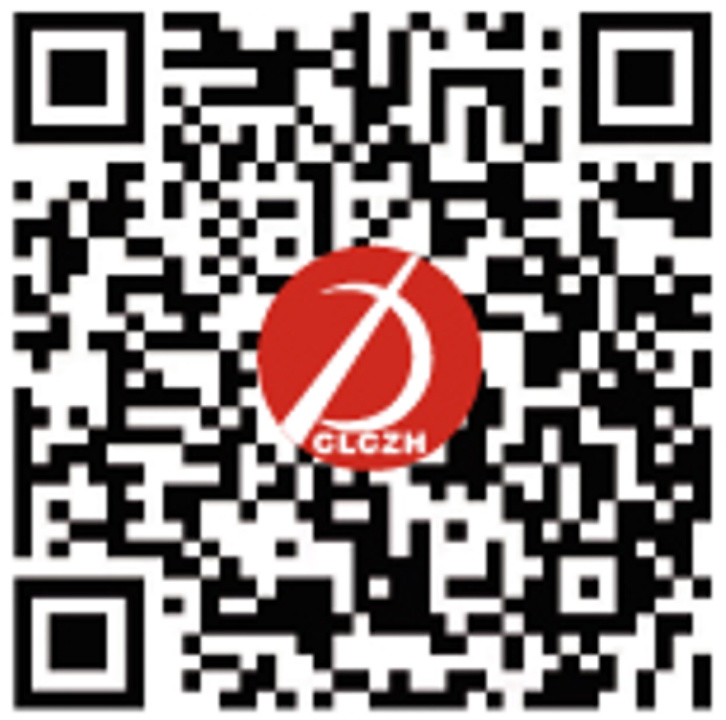
WeChat QR Code
Name: Mr. Chen
Mobile:(86) 156 0271 1777
Telephone:(86-754) 8696 2230
Mailbox:cl@chaolimotor.com
Website:www.chaolimotor.com
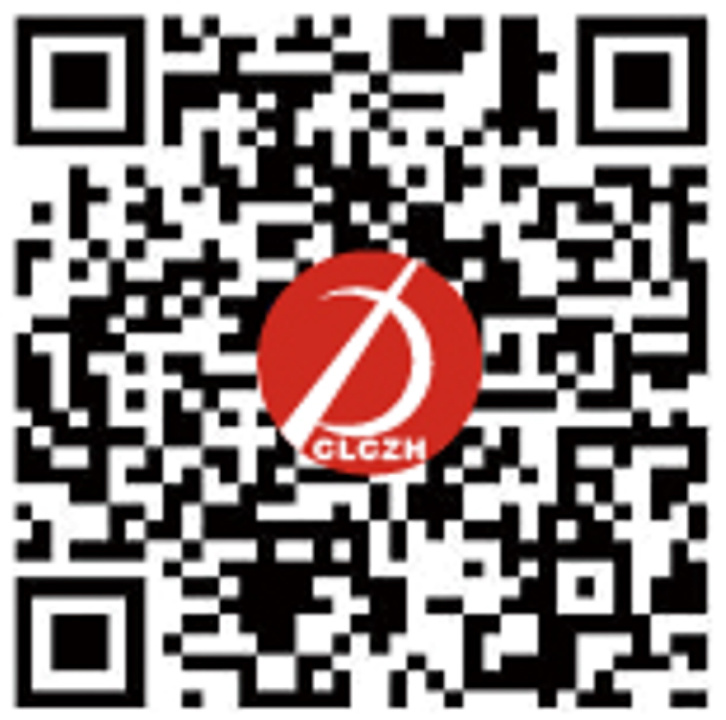
WeChat QR Code
Main Products
Can't find the service you are looking for? Contact us!
If you need to inquire about our products, please leave your email to us and we will contact you within 24 hours.